To Apply DCIO Real Time Optimization Technology, Enhance the
Competitiveness of Chinese Refinery Enterprises
Dr. Jian WANG
OptimiProTM Control Technology Co., Ltd., Beijing£¬ P.R.China
1. Introduction
The demand for oil products declines due to the current financial crisis and therefore the seller¡¯s market is turned to be the buyer¡¯s market. Under such circumstance, the market becomes more competitive and the enterprise production benefit of which is higher will gain more market shares. Consequently, the enterprises should adopt latest technologies, reduce the production cost and improve the production benefit in order to enhance their market competitiveness.
In this presentation, a novel Real Time Optimization (RTO) technology-Dynamic Correlation Integration Optimization (DCIO) technology-which has been successfully applied in the Chinese refinery enterprises, is introduced. By means of the DCIO, the key operating conditions of the reactor of the Fluid Catalytic Cracking Unit (FCCU) are optimized. The liquid yield is increased by 1% and the annual economic benefit is higher than 80 Million RMB on the basis of long-term statistical ledger.
In the process of production, on-line tuning the key operating conditions of the process , maximizing the objective functions, such as yield and benefit, are the task of the Real Time Optimization. The traditional Real Time Optimization is based on process modeling, through which the mathematical description of the optimized process is acquired and moreover the optimal operating points for the current situation are calculated on line by using the computer.
The traditional process modeling is basically built through two ways:
1£©Mechanism modeling: build the mathematical model of each unit by means of the basic equations in respect of chemical industry, such as reaction mechanism, thermodynamic equilibrium and mass balance; afterwards the mathematic description of whole unit is obtained by integrating each unit models.
2£©Data modeling: obtain test data of the device by means of the daily operation data, or by arranging certain tests, and then build the empirical model based on the statistics method.
Obviously, this technology encounters two unavoidable problems which hinder its wide application.
1. It is not simple to build a model, as may be for reasons below:
- Huge and complicated system
- Basic mechanism being not clear, which is common in the process of chemical reaction.
- Super-high modeling cost
2.The built model needs to be modified and maintained frequently. The model itself always has certain scope of application, therefore, if the raw material change and/or the production units reformation of the production process worsen the model error and even result in failure, parameters and/or construction of the model need to be modified. Such actual problem has been always hindering long-term application of the on-line optimization.
Obviously, if there is a way by which the two above-mentioned problems can be solved, it will be a significant progress of the online optimization technology.
Such a way can be the Dynamic Correlation Integration Optimization technology. This technology is developed through dedicated theoretical research and application research for over twenty years. After conquering so many difficulties, the long-term industrial application is finally realized. This technology is admitted by users and has achieved remarkable economic benefit.
2. Dynamic Correlation Integration Optimization Technology
2.1¡¡Basic Theory
The Dynamic Correlation Integration Technology is based on the correlation integration theory. The correlation integration is a random process related operation. In the correlation integration theory, the objective functions, the disturbance variables and the optimized variables are supporsed as random processes. The optimized variables are mean controllable, which are generally represented as:
¡¡¡¡¡¡¡¡¡¡¡¡¡¡¡¡¡¡¡¡¡¡¡¡¡¡¡¡¡¡¡¡¡¡¡¡¡¡¡¡¡¡¡¡¡¡¡¡¡¡¡¡£¨1£©
Thereinto, ¡¡is the mean controllable tuning variable of the m-dimension, ¡¡is the disturbance variable and is the unknown mapping. The optimal objective function is defined as:
¡¡¡¡¡¡¡¡¡¡¡¡¡¡¡¡¡¡¡¡¡¡¡¡¡¡¡¡¡¡¡¡¡¡¡¡¡¡¡¡¡¡£¨2£©
Thereinto, ¡¡is mean of the optimized variable, which may be either setpoint or value position of the base controller. With respect to the optimization of the single variable, it can be proved that, under certain conditions, the gradient of mean of the objective function related to mean of the optimized variable ¡¡could be described by following equation:
¡¡¡¡¡¡¡¡¡¡¡¡¡¡¡¡¡¡¡¡¡¡¡¡£¨3£©
Thereinto, is the noise item with the zero-mean, is the cross correlation integration between the optimized variable and the objective function, is the self-correlation integration of the optimized variable, as shown in formulas £¨4£©and£¨5£©:
¡¡¡¡¡¡¡¡¡¡¡¡¡¡¡¡¡¡¡¡¡¡¡¡¡¡¡¡¡¡¡¡¡¡¡¡£¨4£©
¡¡¡¡¡¡¡¡¡¡¡¡¡¡¡¡¡¡¡¡¡¡¡¡¡¡¡¡¡¡¡¡¡¡¡¡£¨5£©
¡¡and are constants.
In formulas above, are the measured values respectively for the optimized variable and the objective function. It can be seen that ¡¡would be calculated by using the observed values, and therefore based on the formula of
¡¡¡¡¡¡¡¡¡¡¡¡¡¡¡¡¡¡¡¡¡¡¡¡£¨6£©
Gradient of the objective function can be estimated by means of the least square method.¡¡
After the gradient of the objective function is calculated, new setpoint of the optimized variable can be calculated by means of the direct iterative algorithm
¡¡¡¡¡¡¡¡¡¡¡¡¡¡¡¡¡¡¡¡¡¡¡¡¡¡¡¡¡¡¡¡¡¡¡¡¡¡¡¡¡¡¡¡¡¡¡¡£¨7£©
Thereinto, is a constant.
Such iterative process is continuing on line till the gradient turns to be zero, as shown in Figure 1.
The above-mentioned method can also be extended to multivariable case.
In summary, the entire algorithm consists of four steps:
- To sample the dynamic trends of optimized variables and the objective functions
- To calculate the dynamic correlation integration of these trends
- To obtain the gradients between the optimized variables and the objective function through analyzing dynamic correlation integration matrix
- To adjust the optimized variables according to directions and values of the gradients, and then turn to i.
The above four steps shall be continuously repeated. If the gradient is zero, the setpoint shall be fixed, that is:
us(l+1)=us(l)
In the event the system characteristics change due to certain reason, such as raw material change, the gradient will also change and deviate from zero. Therefore, re-tuning of the optimal operating point shall be carried out according to the formula (7) till new optimal point is acquired, as shown in Figure 2.
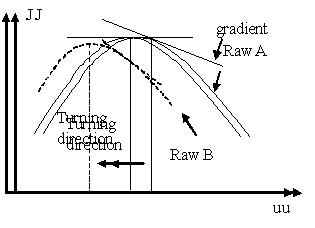
Figure 1: tuning process of optimized variable u
Figure 2: tuning process of optimized variable u after the material change
2£®2 Features of Correlation Integration Optimization Technology
The correlation integration optimization technology has following features which are different from the former technology:
- It is not necessary to pre-build static and dynamic process models.
- It has extremely strong self-adapting capability. It can automatically trace the optimum in the event of change of process conditions, such as raw material change and equipment reformation, etc.
- To make use of the natural fluctuation in the normally operating process for work, and no additional test signal is to be added in the process; therefore, the disturbance to the process operation is very small.
- This technology rejects to disturbances strongly. It works even under the strong dynamic interference, that is, it still works well even if extent of the change resulting from other factors, such as raw material properties, is larger than the wanted signal (the change in objective function result from optimized variable).
- This technology is characteristic of strong robustness. It still works when the dynamic and static properties of the process are drifting.
- It is maintenance free.
- The key operating conditions can be turned to the optimum smoothly so that the safety of the production process is guaranteed.
- The calculated amount is large, so assistance of DCS is required.
2£®3¡¡Conditions for Applying Correlation Integration Optimizer
From the point of view of principle, the correlation integration optimization technology can be applied for the process with following conditions£»
- It must be continuous production process. This technology can not apply to the batch process.
- The optimized objective function should be measured or calculated on line. Since the dynamic correlation integration requires the continuous curve of the objective along with the time, the assay data of the laboratory changing once several hours can not be used.
- The process is controlled by DCS. Since the real time optimization is carried out a 24-hour continuous closed loop, it requires a computer control system with very high reliability. Therefore, the distributed control system (DCS) can be used to meet this reliability requirement.
3.¡¡A Sample Case: Real Time Operation Optimization of Reactor of FCCU
Real time optimization of reactor of the fluid catalytic cracking unit is highly difficult. The challenge is how to automatically trace the optimum in the event of material properties change, device reformation and catalyst renewal, etc. without any manual intervention, such as re-modeling and parameter modifying, etc. The sample case, introduced in this presentation, has adopted the dynamic correlation integration optimization technology and therefore has realized the self-adapting real time optimization.
The fluid catalytic cracking unit in this case has adopted the MIP-CGP (Maximizing Iso-Paraffins¡ªCleaner Gasoline and Propylene) technology, developed by the Research Institute of Petroleum Processing of SINOPEC, and its designed processing capability is 1.4Mt/a.
3£®1¡¡Objective Function and Optimized Variable
Optimized objective function of the catalytic cracking unit is diversified. The multi-processing scheme optimization is adopted for the real time optimization in this presentation, that is, the optimized objective function can be switched as required.
According to situation of the current oil products sales market, the entire real time optimization system is capable of adapting different raw materials for processing and producing different main products because of the diversified scheme of fluid catalytic cracking processing. This real time optimization system can adapt for five processing schemes:
- The optimization scheme with liquid hydrocarbon as the main product, the 8-hour accumulative yield of the liquid hydrocarbon is the objective function, and the diesel oil yield can be controlled not less than certain setting value.
- The optimization scheme with gasoline as the main product, the 8-hour accumulative yield of the gasoline is the objective function, and the diesel oil yield can be controlled not less than certain setting value.
- The optimization scheme with diesel oil as the main product, the 8-hour accumulative yield of the diesel oil is the objective function, and the liquid hydrocarbon yield can be controlled not less than certain setting value.
- The optimization scheme focusing on total liquid yield, and 8-hour accumulative yield of liquid hydrocarbon + gasoline + diesel oil is the objective function.
- The optimization scheme focusing on overall economic benefit of the FCCU, and the economic benefits achieved by processing each ton of raw materials within 8 hours are calculated according to prices of the current raw materials and products.
In the event of choosing the optimized variables, those significant and easily controllable variables in the reaction-regeneration process should be mainly taken into consideration. In this fluid catalytic cracking unit, the following variables are used as on-line optimized variables:
- Reaction temperature of the first reactor
- Catalyst inventory in the second reactor
- Pre-lifting stem (stem pre-lifting process)
- Pre-lifting dry gas (dry gas pre-lifting process)
- Residuum ratio
- Feed temperature
- Flow of termination agent
- Cycle oil ratio
- Slurry oil cycle ratio
- Added amount of fresh catalyst
The real time optimization system is a two layer control system in logical. It calculates the setpoints of the optimized variables, and then sends them to the remote setpoints of PID control loops in DCS for implementation. The sampling period and the control period of the optimization system are respectively 1 minute and 10 minutes.
Long-term Operation and Discussion
After the system is put into operation, it is widely concerned in all respects due to its excellent performance and significant benefit. Since the put-into-operation in March, 2007, the system has been kept operating continuously except for short-time off-line due to mechanical reason. Operating environment and stability of the unit are largely improved, and the benefit is increased.
The author has compared the statistical mass balance for three months before and after the put-into-operation, and the comparison result is shown in Table 3.1:
Table 3.1: Statistics of Yield Change of Different Products Before and After the Put-into-operation
Product
£¨%£© |
Before
£¨%£© |
After
£¨%£© |
Amount£¨%£©£¨after-before£© |
Dry gas |
3.71 |
3.89 |
0.17 |
Liquid hydrocarbon |
22.21 |
24.52 |
2.31 |
Of which£ºpropylene |
6.72 |
7.34 |
0.62 |
Gasoline |
36.40 |
36.78 |
0.38 |
Diesel oil |
22.08 |
20.46 |
-1.62 |
Slurry oil |
6.67 |
5.52 |
-1.15 |
Coke |
8.50 |
8.45 |
-0.05 |
Loss |
0.43 |
0.38 |
0.05 |
Total liquid yield |
80.69 |
81.76 |
1.07 |
Convert ratio |
71.25 |
74.02 |
2.77 |
From the table 3.1, it can be seen that, after the dynamic correlation integration optimization technology is applied, the coke yield of reaction obviously declines, the total liquid yield rises dramatically. Since the coke yield of reaction declines, the control of dilute phase/dense phase temperature of the regenerator become more smooth and reasonable.
The catalyst is added in balanced way, the activity is stable and the unit consumption declines.
Flow of pre-lifting steam is automatically controlled by the control valve according to the demand of reaction optimization, consequently making concentration of the propylene in the liquid hydrocarbon rise.
Since the coke rate of reaction declines, the reaction depth can be further strengthened. The yield of gasoline and liquid gas is improved obviously, and the yield of light diesel oil obviously declines, consequently realizing the purpose of producing more propylene through catalytic cracking.
After long-term and continuous optimization and operation inspection, the effect becomes more obvious and the economic benefit of the unit increases. According to the statistics, the annual economic benefit will achieve 80 Million RMB after the optimization.
Conclusion
As a novel on-line real time optimization technology, the dynamic correlation integration optimization technology, with the support of the Ministry of Science and Technology of the People¡¯s Republic of China and the Beijing City Government, has obtained a number of patents and correlative certificates, which have actively supported the research and development of this technology.
Compared with the traditional real time optimization, especially the modelling free and the self-adapting the raw material change and device reformation, the dynamic correlation integration optimization technology has many attractive features, and it can largely improve the long-term operation rate of the on-line optimization. Since this technology could be applied in most oil refining processes, it has wide application future and therefore it could obtain the economic benefit of the Chinese refinery enterprises and also enhance their competitiveness. |